Optymalizacja Layoutu Magazynu dla Potrzeb Logistycznych
Współczesna logistyka wymaga elastycznych i wydajnych rozwiązań magazynowych, które są odpowiedzią na dynamicznie zmieniające się potrzeby firm. Jednym z kluczowych aspektów optymalizacji procesów magazynowych jest dostosowanie layoutu obiektu do specyficznych wymagań. Projektowanie nowego układu magazynu to proces kompleksowy, który może znacząco zwiększyć efektywność operacyjną, obniżyć koszty i zredukować liczbę błędów.
Definicja Layoutu Magazynu
Layout magazynu to koncepcja organizacji przestrzeni magazynowej, obejmująca kwestie technologiczne i procesowe. Może dotyczyć:
- Budowy nowego magazynu,
- Rozbudowy istniejącego obiektu,
- Reorganizacji aktualnego układu.
Jego głównym celem jest optymalizacja przepływów towarowych, poprawa dostępności towarów, minimalizacja zbędnych operacji i maksymalizacja efektywności pracy. Dzięki odpowiedniemu projektowi można zmieścić więcej towarów w tej samej przestrzeni, skrócić czas realizacji procesów oraz ograniczyć koszty operacyjne.
Kluczowe Zasady Projektowania Layoutu Magazynu
1. Indywidualne podejście
Każdy projekt powinien być dostosowany do specyfiki firmy, jej branży, rodzaju asortymentu, przewidywanego wzrostu sprzedaży i zmian w modelu dystrybucji. Nie istnieją uniwersalne szablony layoutów - kluczowe jest bazowanie na danych i szczegółowych analizach.
2. Planowanie na przyszłość
Podczas projektowania nowego układu należy uwzględniać prognozy rozwoju firmy na najbliższe 3-5 lat. Dotyczy to powierzchni, liczby pracowników, systemów przechowywania i innych zasobów. Przy zmianie istniejącego layoutu należy uwzględnić ograniczenia wynikające z budowy obiektu.
3. Kompleksowe podejście
Zmiana layoutu powinna być częścią szerszej transformacji magazynu, obejmującej optymalizację procesów oraz aktualizację systemów IT. W ten sposób można maksymalnie wykorzystać potencjał nowego układu.
Redesign Stref Magazynowych
Każdy magazyn składa się z czterech głównych stref:
- Przyjęcia (wejścia): Odbiór i weryfikacja towarów.
- Składowania: Przechowywanie towarów zgodnie z ich wymaganiami.
- Kompletacji: Przygotowanie towarów do wysyłki, co pochłania największą ilość czasu i zasobów.
- Wydań (wyjścia): Przygotowanie i załadunek towarów do transportu.
Optymalizacja stref często obejmuje oddzielenie przyjęć od wydań, co eliminuje krzyżowanie się strumieni towarowych. Taki układ zmniejsza ryzyko zakłóceń i pozwala na lepszą organizację pracy.
Projektowanie layoutu magazynu to złożone zadanie wymagające analizy i długoterminowego planowania. Odpowiednio wdrożony układ przestrzenny zwiększa wydajność, redukuje koszty i wspiera rozwój firmy. Ważne jest jednak, aby pamiętać, że nowy layout to jedynie część większej zmiany, obejmującej także procesy i systemy zarządzania magazynem.
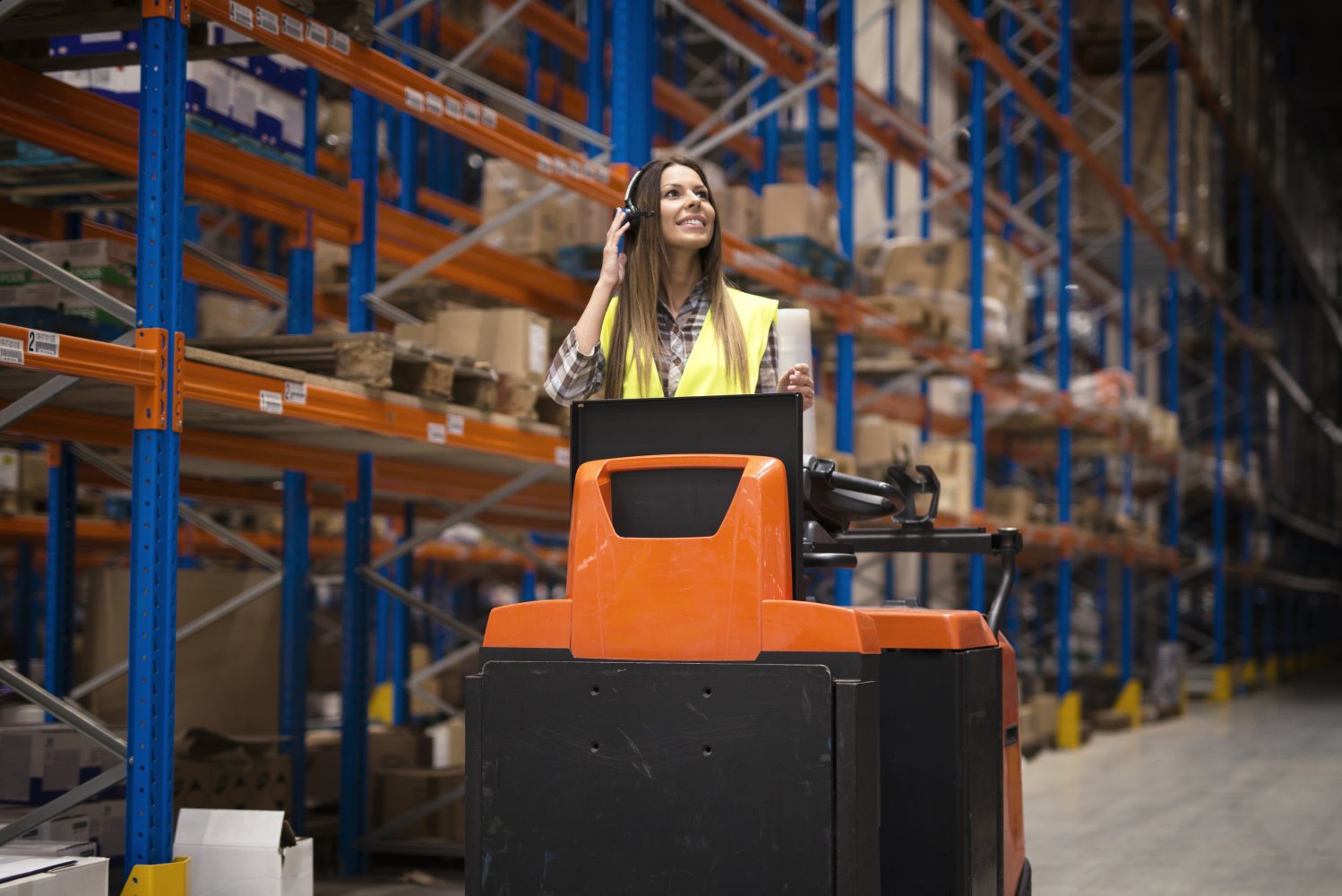
Optymalizacja procesów magazynowych - klucz do lepszej efektywności
Procesy magazynowe to uporządkowane operacje, które mają kluczowe znaczenie dla sprawnego funkcjonowania magazynu. Ich optymalizacja pozwala na poprawę wydajności, szybkości i dokładności działań. Wszystkie operacje w magazynie są ze sobą ściśle powiązane, a ich efektywność przekłada się bezpośrednio na jakość obsługi klienta i koszty operacyjne.
Procesy magazynowe można podzielić na kilka podstawowych grup:
- przyjęcie (rejestracja i rozłożenie towarów),
- składowanie,
- uzupełnianie zapasów w miejscach kompletacji,
- kompletacja zamówień,
- kontrola i pakowanie,
- wyjście towarów (załadunek),
- procesy wewnętrzne (np. obieg dokumentów),
- procesy dodatkowe (VAS, np. copacking).
Każdy z tych procesów wymaga analizy pod kątem wydajności i zgodności z wymaganiami operacyjnymi. Ważne jest, by nie tylko działały poprawnie, ale były realizowane optymalnie, minimalizując błędy, czas i koszty.
Priorytet: optymalizacja przyjęcia towarów
Proces przyjęcia towarów stanowi fundament dalszych operacji magazynowych. Jego błędy mogą generować kaskadę problemów, które często wychodzą na jaw dopiero u klienta. Kluczowym krokiem jest tu przejście na przyjęcie z natury, czyli weryfikację dostarczonego towaru bez sugerowania się dokumentami. Magazynier samodzielnie wypełnia dokumentację na podstawie fizycznie zliczonych towarów. Dzięki temu:
- Ograniczamy błędy - unikamy efektu "potwierdzania zgodności", który występuje przy bazowaniu na gotowych dokumentach.
- Przyspieszamy proces - operacje są niezależne od biurokratycznych opóźnień.
- Minimalizujemy ryzyko nadużyć - brak informacji o oczekiwanej ilości towaru utrudnia kradzież nadmiarowych produktów.
Eliminacja krzyżowania się strumieni pracy
Wielu problemów w magazynie można uniknąć poprzez skuteczne rozdzielenie strumieni pracy. Fizyczne lub organizacyjne oddzielenie procesów przyjęcia od wyjścia towarów eliminuje ryzyko błędów załadunkowych i zwiększa bezpieczeństwo operacji. Można to osiągnąć:
- Fizycznie - rozdzielając strefy magazynowe np. ścianami.
- Systemowo - wprowadzając zmiany w systemach zarządzania magazynem (WMS).
- Czasowo - planując oddzielne godziny dla procesów przyjęcia i wysyłki.
Poprawa organizacji procesów magazynowych to wyzwanie wymagające zaangażowania i ciągłego doskonalenia, ale jej efekty w postaci lepszej wydajności i jakości są tego warte.
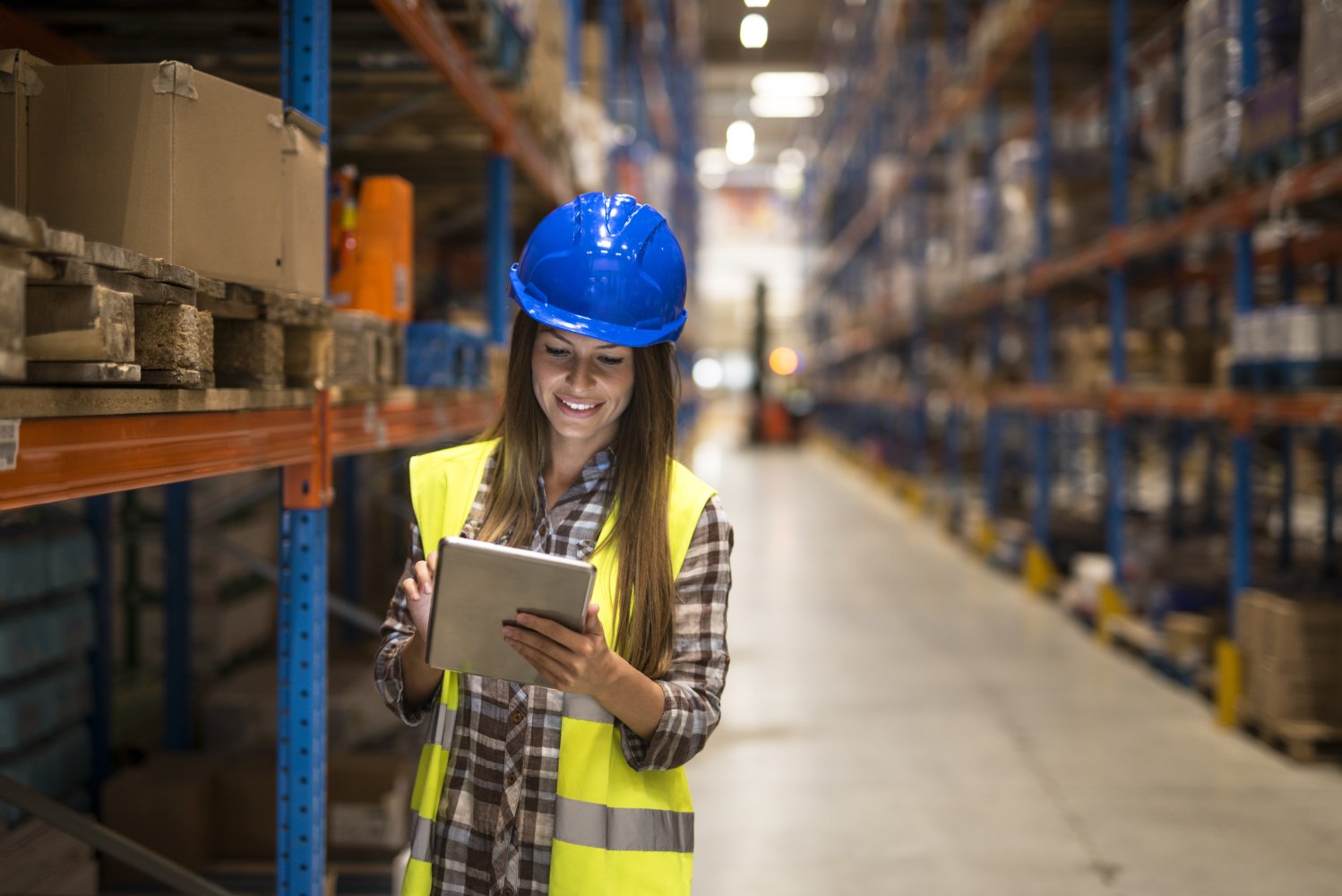
Systemy zarządzania magazynem, takie jak WMS (Warehouse Management System) oraz WES (Warehouse Execution System), stanowią istotny element nowoczesnego zarządzania magazynem. Ich główną rolą jest kontrola, koordynacja oraz optymalizacja procesów magazynowych, co w konsekwencji wpływa na efektywność operacji i przewagę konkurencyjną firmy.
Różnice między systemem WMS a WES
System WES różni się od WMS tym, że działa jako nakładka na nadrzędny system ERP, umożliwiając wdrożenie poszczególnych funkcji bez konieczności modyfikacji całości operacji magazynowych. Daje to możliwość usprawnienia tylko wybranych procesów, co jest idealne dla firm potrzebujących elastycznych i szybkich rozwiązań w konkretnych obszarach. Natomiast WMS obejmuje kompleksowo wszystkie operacje magazynowe, zapewniając wsparcie zarówno operacyjne, jak i zarządcze, i jest dedykowany przedsiębiorstwom, które dążą do pełnej integracji i standaryzacji procesów magazynowych.
Dobór systemu WMS dostosowanego do specyfiki magazynu
System WMS nie powinien być szablonowym narzędziem, lecz dostosowanym do indywidualnych potrzeb danego magazynu. Wybór systemu projektowanego we współpracy z logistykami, którzy dobrze rozumieją realia branży, przynosi firmom większe korzyści, niż zakup ogólnego rozwiązania zaprojektowanego wyłącznie przez programistów. Systemy dostosowane do specyficznych wymagań i przepływów pracy mogą znacząco wpłynąć na poprawę wydajności operacji magazynowych i dać firmie przewagę konkurencyjną.
Standaryzacja procesów
Wprowadzenie standaryzacji procesów w systemie WMS pozwala na uproszczenie i usprawnienie działań magazynowych. Standaryzacja ułatwia pracę personelu i sprawia, że wykonywane przez nich czynności są powtarzalne i bardziej efektywne. Przykładem jest ujednolicenie procesu kompletacji, gdzie system WMS automatycznie optymalizuje ścieżkę pobrania towaru - niezależnie od specyfiki zamówienia. Taka standaryzacja, umożliwiająca magazynierom sprawną realizację zleceń, przyczynia się do bezbłędności i szybszego wykonywania operacji.
Efektywny magazyn
Zwiększenie efektywności magazynu to proces, który wymaga przemyślanego podejścia i ciągłego doskonalenia. Optymalizacja layoutu, usprawnienie kluczowych procesów oraz dobór odpowiedniego systemu zarządzania magazynem to tylko niektóre z działań, które mogą przynieść wymierne korzyści. Wdrażając te rozwiązania, firmy nie tylko poprawiają swoje wyniki, ale także budują przewagę konkurencyjną na rynku. Efektywny magazyn to fundament nowoczesnej logistyki i satysfakcji klientów.
Napisz komentarz
Komentarze